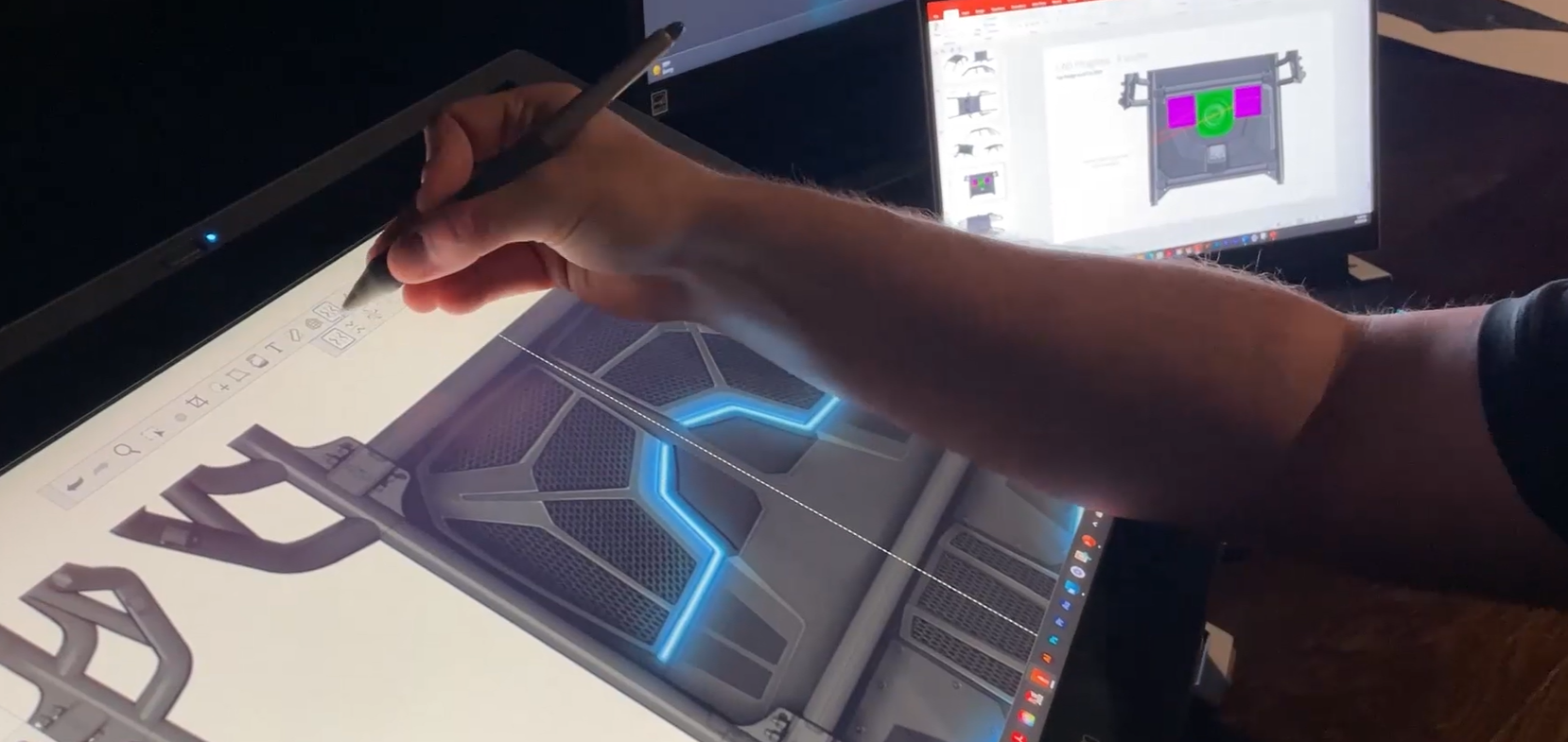
Industrial Product Design
Industrial Design
Specializing in delivering product solutions - both innovative and highly functional, with a user first mindset. Our industrial design process involves POC modeling and testing ideas using 3D printing, prototyping, and validation models for user evaluation. We combine functionality, aesthetics, and brand to create inspiring product experiences for any industry.
There are a variety of different tools and processes we use within the industrial design stage. Every project has its own goals and requirements – we help provide value by recommending which tools and processes are an appropriate fit to meet the needs of your project. To drive innovation, our industrial designers implement the most fitting design methodologies to construct a range of technical concepts.
PRODUCT AESTHETICS
The creation of a visually appealing design is one of the highlights of the design process. Elements of aesthetically pleasing products include form, shape, color, material, texture, finish, accent details, and branding integration. Balancing the visual elements of a product with its functionality, ergonomics, and manufacturing feasibility is an art. The phrase “form follows function” rings true, although it is the form that typically first engages users.
A strong industrial product design aesthetic encompasses the right design elements and principles - when executed properly, this creates visually pleasing and emotionally engaging products. This creativity is the culmination of strategic and tactical activities our industrial designers use for creating solutions that stand out from the competition.
HUMAN FACTORS AND ERGONOMICS
Understanding how people connect with systems, products, and environments provides valuable insight for designing products that are intuitive, easy to use, and efficient. This requires a foundation of user research and comparative product research. Human factors aim to minimize risk and potential errors that human interaction could have.
The goal of ergonomics is to make sure the products and systems being designed fit the physical capabilities and limitations of individuals - this includes considerations of shapes, sizes, controls, and interfaces. Before applying aesthetic ideas to a product design, an industrial designer must understand the interaction details that users will be performing.
DESIGN VALIDATION MODELS
Validation models provide a pragmatic means to assess the viability of a conceptual design. We create prototypes quickly with straightforward means, serving the singular purpose of determining whether a particular concept merits further development. These models do not include details such as final materials, color, or finishes, and sometimes they don't reflect size or scale.
In instances where the concept involves functionality, more sophisticated approaches may be employed, such as kit-bashing existing products to replicate the intended function within the specific context of the concept. This dynamic approach allows for a focused evaluation of key design elements, ensuring that the concept aligns with intended goals before progressing to more intricate phases of development and engineering.
CAD DEVELOPMENT
Our approach to CAD development is carried throughout the creative operation. It is an efficient means to create, analyze, and refine designs in a digital environment before generating functional prototypes. There are various levels of CAD development used throughout industrial product design. Our goal is to use this tool only when it provides necessary value, as an aid to the creation process and as a means to provide handoff material for engineering teams and manufacturers.
While developing products, CAD software helps industrial designers work with mechanical engineers to ensure ideas do not directly contradict the goals of each discipline. Multidisciplinary teams must have the same goal throughout the creative process, and CAD models are often used in the communication process to help align these goals.
CONCEPTUAL BOM
Creating a conceptual Bill of Materials (BOM) during the design phase of development is a crucial step in effectively managing product costs - whether aiming for a budget or premium-driven solution. Often, cost considerations are not closely monitored until later in development, potentially resulting in unexpected cost challenges and sticker shock. By establishing a preliminary BOM at the outset, we proactively address cost implications, mitigating the risk of unforeseen expenses. This ensures a more transparent and controlled development for future manufactured objects.
It is critical to understand the manufacturing processes that are valid options early on. Some products are suited for mass production, and others have tighter production costs which will limit manufacturing options. As a design is refined in the implementation stage, cost ranges are tuned. Fewer surprises in the production process support a more sustainable product development journey.
EXPERIENCE AND INTERFACE DESIGN
Products are enhanced through strong interactions and overall user satisfaction. A cohesive, user-centric experience successfully accommodates user behaviors, emotions, and motivations. Whether there is a user interface (UI) or not, all products have visual and interactive elements that require direct engagement. There is an interactive operation and particular purpose that the user must be guided through to ensure a smooth user experience (UX). This experience should be simplistic and user-friendly, providing an intuitive path from beginning to end.
Aesthetically pleasing products created by industrial designers can help enhance user experience, but other factors such as iconography and instructions built by graphic designers or other related disciplines are just as important. A new technology or unique way of implementing existing technology can create an innovative user interface that serves as the defining element of a new product.
COLOR, FINISH, MATERIAL (CFM)
A product’s aesthetics are enhanced by its surface properties of color, finish, and material. A positive emotional connection between the user and product is created with careful selection and implementation of these properties. CFM decisions are made based on the intended purpose and design preferences of the product - these are often correlated with pre-existing brand standards.
Often created for evaluation in a design presentation, CFM details are a highlight of the industrial designers focus, as these are the final touches of their product designs. This requires an understanding of manufacturing processes, the types of materials that can be used, and the manufacturers that could be used for production. Strong CFM documentation helps with handoff to engineers to clearly communicate the execution of design intent. Another important element used during this stage is incorporating a visual brand language (VBL) that branding strategists have defined.
RENDERINGS
Used for a wide range of purposes, rendering is the visual representation of a product solution. Utilizing digital models with computer software and transforming them into photo-realistic or styled images can be appropriate at both early and later stages of development. Whether used as marketing collateral, a pitch to investors for further funding, or for design reviews to evaluate product direction, renderings are an effective high-value tool in industrial product design. Before creating manufactured products, renderings are a high-value tool to evaluate market placement.
VERIFICATION PROTOTYPE
Functional prototypes are models that convey functionality while looking good! In most cases, these are the most effective and valuable type of prototyping. Not only are these models best suited in the hands of the end user, they also give assemblers, service teams and technicians an opportunity to provide feedback during signoff. The processes for creating prototypes are based on use and what they are trying to achieve.
Nothing is limited - CNC, 3D printing, casting, and forming techniques are all viable options. But know your customer and don't assume they will regard the prototype the same as you! Our product designers often incorporate our implied engineering process to construct these models. This helps save time, while providing a level of detail that closely simulates manufactured parts.
FAQ’s
-
This question is asked often, and it is really difficult to pinpoint an answer because there are so many variables, from product complexity, testing, user/focus group feedback, certifications, etc. In a perfect world, we recommend our clients allocate up to 8-15 weeks, depending on the complexity and the speed at which client feedback.
2-3 weeks for research/strategy,
3-4 weeks for industrial design concept development,
3-5 weeks for mechanical development/implementation,
3-4 weeks for prototyping.
In most cases, this doesn’t mean you are ready for tooling!
We will gladly share a case study of our creative process and work - walk through a timeline from start to finish to give you a more realistic timeline for your project. Designing products can look very different depending on business goals and working budget.
-
In many cases, especially larger corporations that produce products, an in-house creative team already exists. One of our strengths is the ability to adapt and challenge the status quo without compromising the creative value you need. Our team of product designers easily adapt to various workflows, and our goal is to find the most effective way to communicate and share ideas between our team members and yours.
-
This question comes up frequently, and giving an exact estimate can be challenging due to the presence of several variables. Nevertheless, in many cases, we segment project estimates into distinct phases to ensure transparency and clarity in assessing the required effort.
-
Our industrial product design team puts a great emphasis on testing and developing products that are meaningful, innovative, and memorable for users. There is not a singular, linear approach to achieving this with every project. Consumers vary greatly from industry to industry, and project goals often change on a whim. Although we try to establish requirements early on to limit changes, it is sometimes unavoidable. This requires our product designers to be agile, so we do not skip a beat with a shifting design process. One of the strongest traits a product designer has is the ability to adapt quickly, but still remain on track with the higher-level project goals. This may require looking for additional resources, or a new technology to help aid in the development process.
-
Yes. We understand the hurdles and complexities that come with launching a new startup or building a brand — it's no small feat. Recognizing the various challenges, we, as partners, are prepared to contribute our design services as a form of capital tailored to the specific needs of the venture.
-
This varies. Our standard payment terms are net 15 days. We offer flexibility to our long-standing clients and established relationships, allowing for a net payment period of 30 days or more.
-
At the beginning of any industrial design project, many preconceived ideas won't materialize or reach fruition. The problem-solving process in new product development is rarely linear. Our objective with any client project is to offer transparency, including risks and opportunities. With a clear goal of providing you with a solution that meets the business objectives and products your customers will love.